Этапы производства радиаторов Zehnder Charleston
Предлагаем вам ознакомиться с процессом изготовления стальных трубчатых радиаторов на примере Zehnder Charleston. Хотя каждый производитель имеет свои особенности (например, только Zehnder использует плотные картонные коробки для упаковки своих радиаторов), процесс производства на всех заводах примерно одинаков.
Этап 1. Поставка стали
Для создания радиатора Zehnder Charleston требуется высококачественная листовая сталь, поставляемая в виде катушек весом более 2 тонн и диаметром 1,5 метра, а также стальные трубы длиной от 4 до 6 метров, поставляемые связками общим весом от 1 до 1,4 тонны. Естественно, все материалы имеют подтверждение соответствия европейским нормам DIN и EN, а также проходят дополнительное выборочное тестирование на производстве.
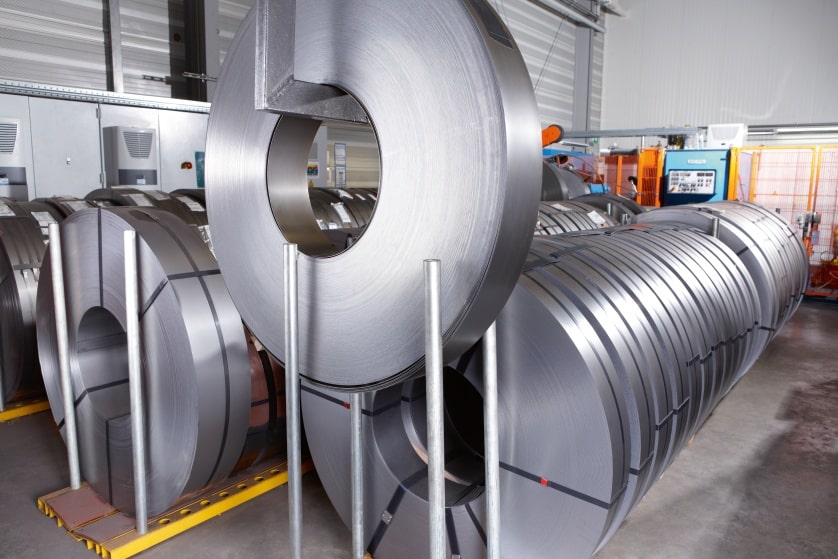
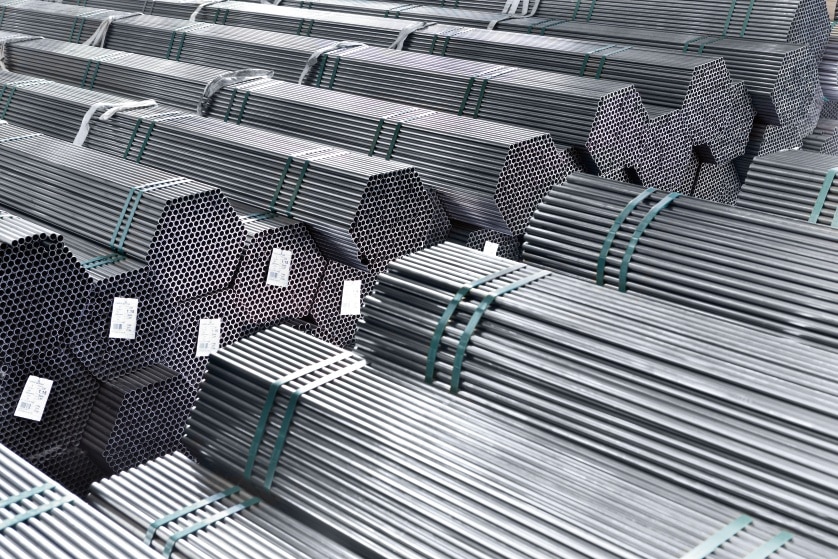
Этап 2. Изготовление коллектора
Чтобы создать коллекторные заготовки для каждой секции, листовую сталь подвергают штамповке при помощи пресса. Затем две половинки коллектора свариваются вместе, формируя верхнюю или нижнюю головку секции радиатора. Процесс лазерной сварки обеспечивает чистую и без окалин сварку головок. Во время полностью автоматического испытания каждая головка подвергается проверке на полную герметичность.
Качество головок также подвергается визуальной оценке. Это позволяет определить, была ли сохранена равномерность шлифования или произошло какое-либо отклонение.
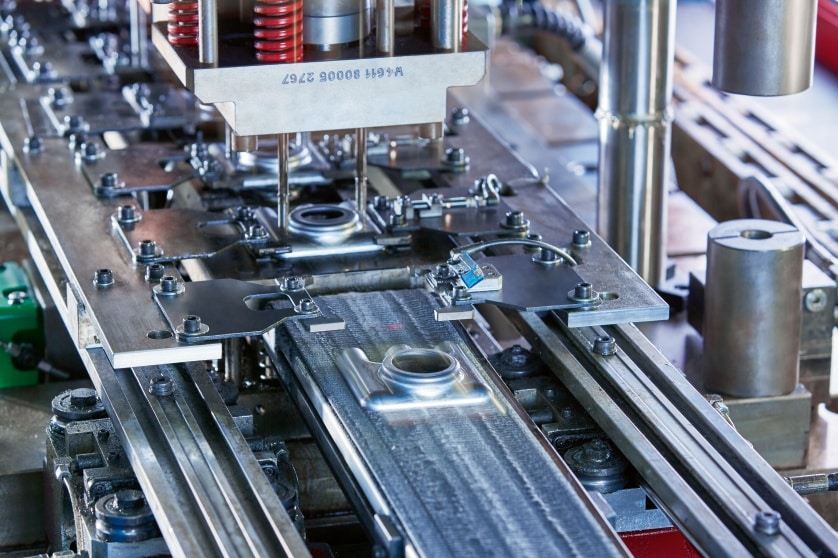
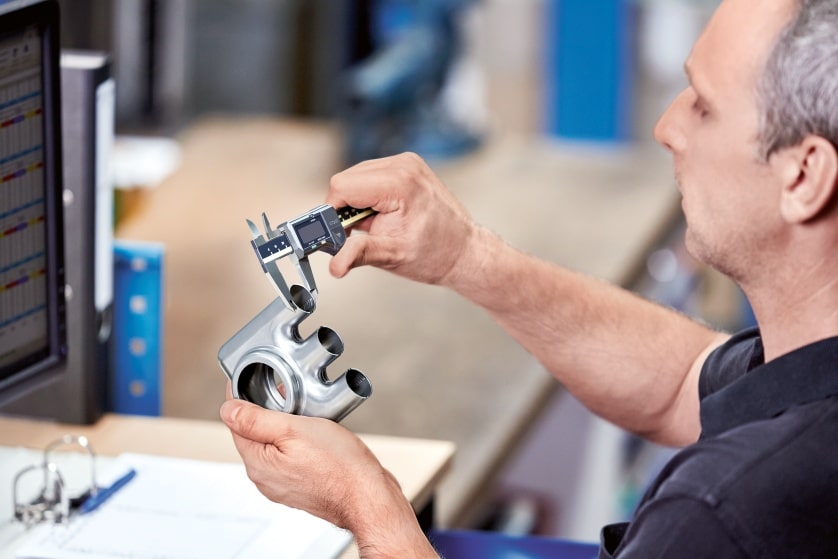
Постоянная проверка с помощью координатно-измерительной 3D-машины исключает даже минимальные отклонения от заданного размера.
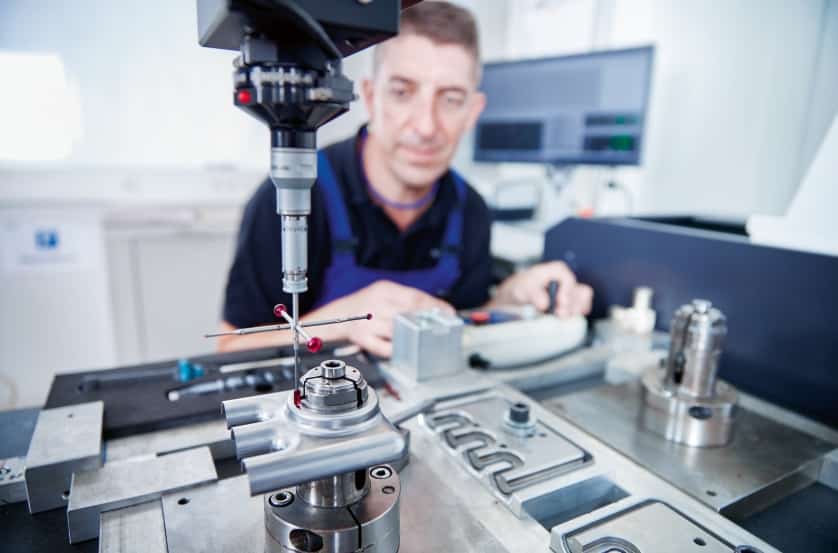
Этап 3. Сварка секций
Коллекторные части и соответствующие трубки свариваются вместе. Благодаря сварочному процессу Zehnder RBS, сварка коллектора и трубок осуществляется без образования окалины. Это обеспечивает оптимальное качество продукции и повышает эффективность производственного процесса. Сварные швы очищаются как с лицевой стороны, так и между трубками, чтобы достичь чистого визуального качества продукции. Контроль качества осуществляется на каждом этапе производства. После сварки трубок к коллекторам и обработки сварных швов, секции проходят проверку на герметичность.
Процесс шлифования осуществляется с помощью автоматизированной системы, однако качество шлифовки всех деталей проверяется сотрудником. Если обнаруживаются какие-либо дефекты, они устраняются вручную. На последнем этапе производства секций из каждого сварочного аппарата отбирается образец и проверяется на наличие утечек. Секция надежно закрывается, затем погружается в бассейн с водой и подвергается воздействию давления воздуха в размере 16 бар для проверки герметичности.
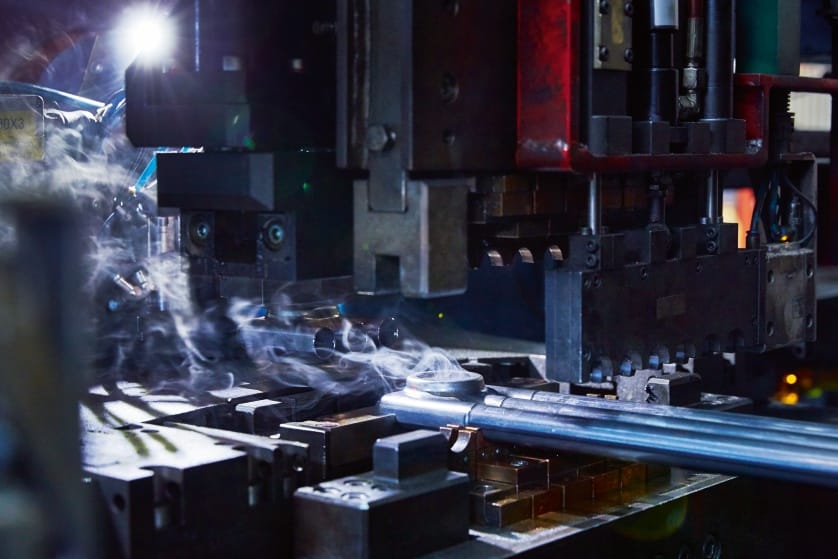
После прохождения этого теста, секции отправляются на промежуточный склад, где хранятся все стандартные типоразмеры.
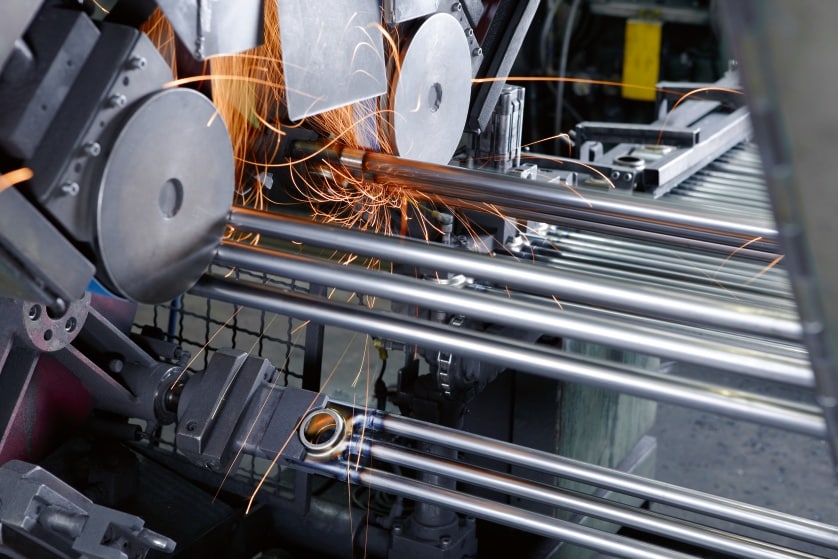
Этап 4. Сборка радиатора
На специальной машине секции радиатора свариваются между собой с использованием точечной сварки. Машина осуществляет сварку секций внутренне на 360 градусов. Точность сварки обеспечивает герметичность радиатора. После этого каждый радиатор проходит проверку на герметичность в специальных ваннах с водой. В радиатор подается воздух под давлением 18 бар для тестирования.
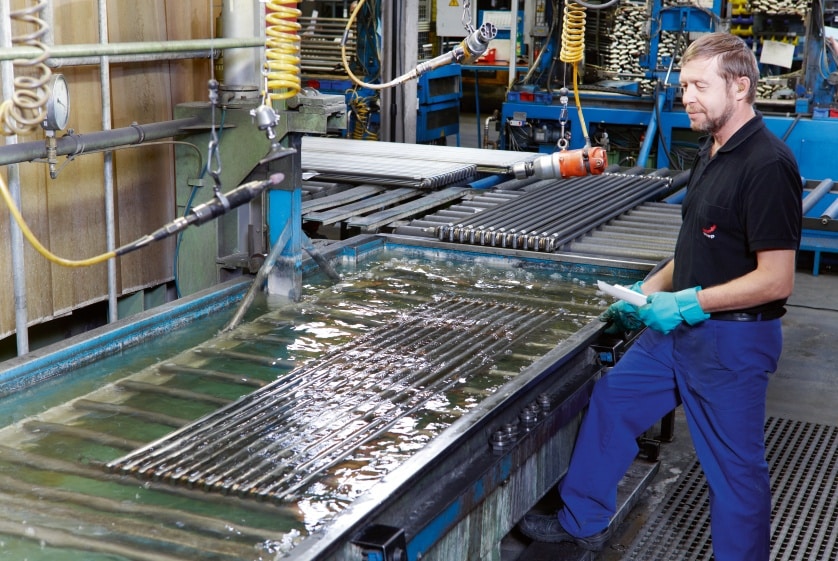
Испытанные радиаторы подвешиваются на автоматизированном конвейере, протяженностью около 2,5 км, и направляются на следующие этапы производства. Радиаторы остаются подвешенными на конвейере до момента упаковки.
Этап 5. Покраска
После испытаний радиатор проходит процедуру щелочной очистки для удаления пыли и грязи. Затем радиатор погружается в ванну с электролитической грунтовкой, которая защищает его от внешней коррозии и подготавливает поверхность для последующей покраски. После этого радиатор помещается в печь, где под действием температуры 180 °C грунтовочный слой закрепляется. Затем радиатор отправляется на следующий этап производственной линии, где наносится порошковое покрытие. Стандартный белый порошок наносится с помощью автоматических камер, а цветные радиаторы получают свои оттенки после ручного нанесения порошка. После этого радиатор снова проходит печь, где при температуре 180 °C порошок превращается в прочное покрытие, обеспечивающее привлекательный внешний вид, защиту от механических повреждений и устойчивость к температурным изменениям.
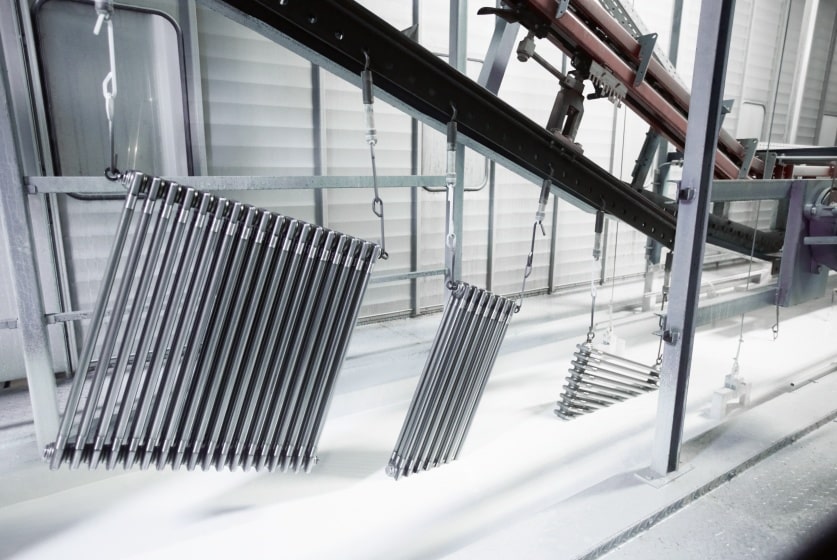
После этого радиатор проходит окончательную проверку качества. Основное внимание при визуальном осмотре уделяется поверхности радиатора, его дизайну (включая индивидуальные подключения) и корректности идентификации модели (соответствие размеров и цвета). Если в результате осмотра выявляются дефекты, радиатор будет направлен на доработку или отбракован.
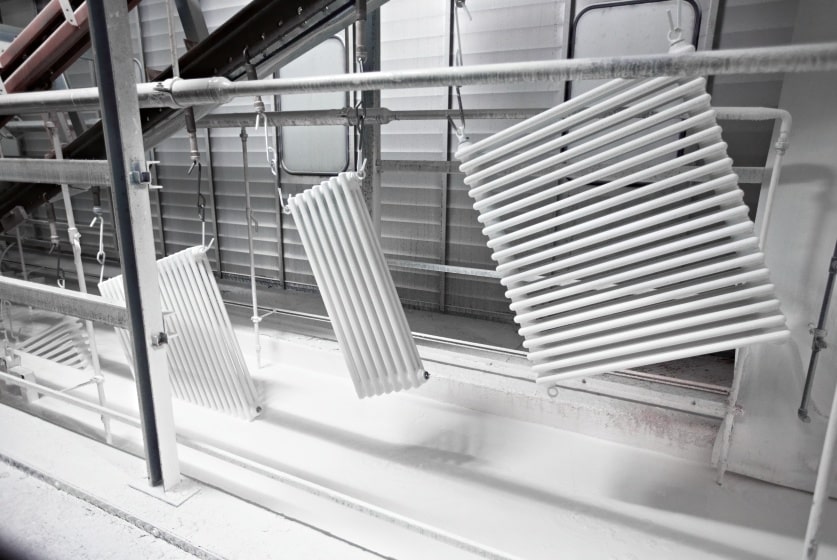
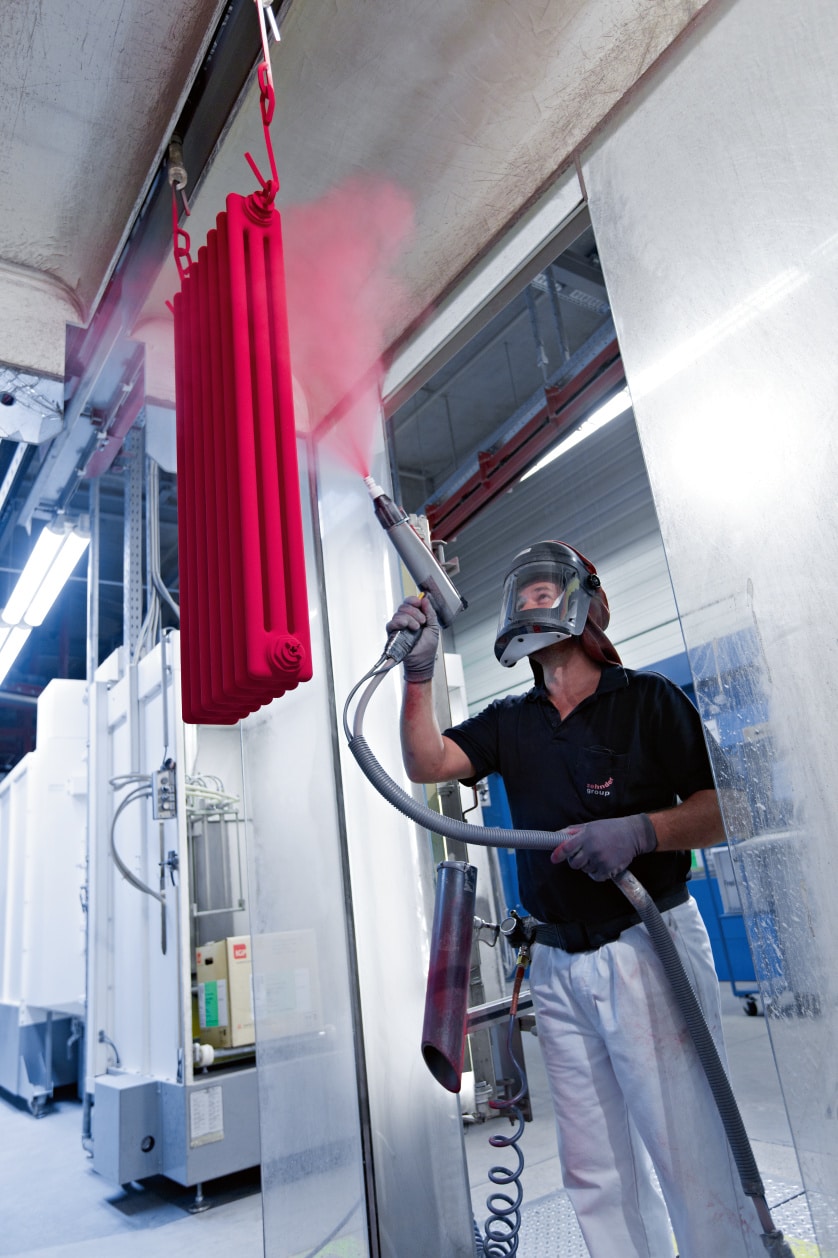
Этап 6. Упаковка
Примерно 95-98% радиаторов Zehnder Charleston упаковываются с использованием полностью автоматизированной линии. Каждый радиатор покрывается качественным многослойным картоном, который полностью охватывает его поверхность, обеспечивая надежную защиту во время транспортировки, хранения и на строительной площадке во время и после монтажа. Каждый радиатор упаковывается в соответствии с заказами клиентов, и они собираются на паллетах. Стабильная картонная упаковка обеспечивает надежную защиту радиаторов даже на строительной площадке до завершения всех строительных работ.
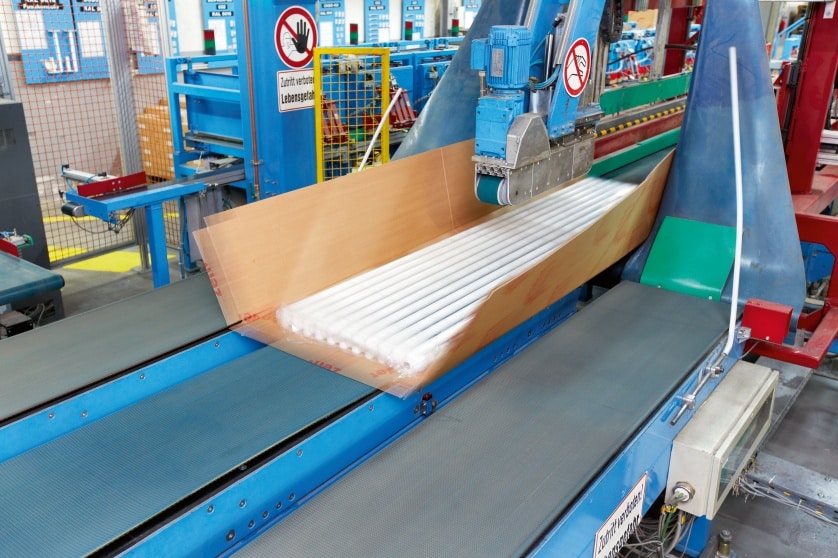
QR-код на упаковке также относится к пленке, показывающей все преимущества картонной упаковки.
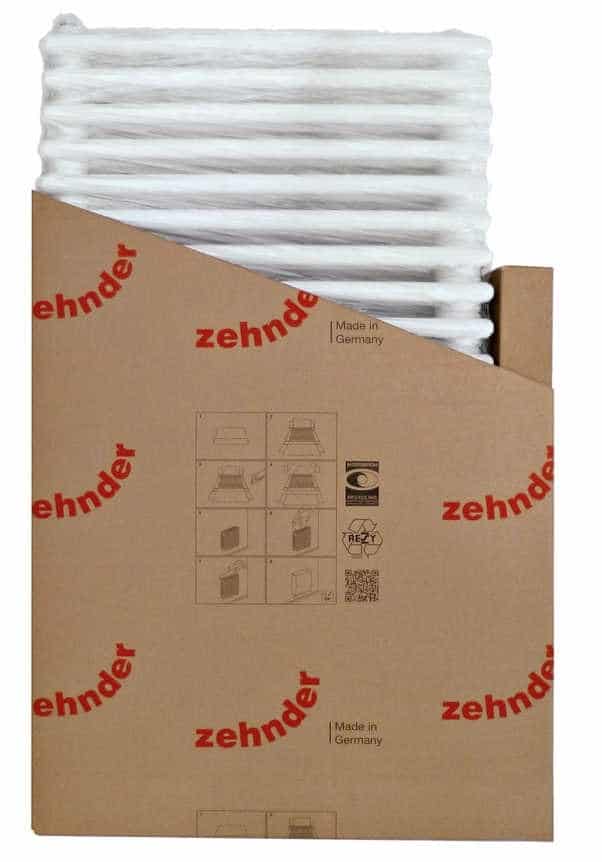